During the month of March, Colibri Spindle is focusing on the most common jet spindle speeder applications and giving our partner insights into the best practices for optimizing success.
This article looks at two case studies as well as our Partners’ recommended cutting tools for engraving.
Engraving is an ideal application for jet spindles and process time savings of 6-12X can be achieved, which is the equivalent of saving 50-80% saving in machining time! For engraving and other applications where small, pointed tools are used, higher speeds are required for a quality finish and productive feed rates.
Depth of cut (Ap) is usually less than 0.5 mm and width of cut (Ae) is very narrow as well, usually less than 1 mm. Cutting Edge Angle varies between 45 to 60 Degree. The letters and numbers are integrated to engrave and so what we are looking for are accuracy, speed, and minimal power. Ideal machining requirements for Jet Spindles.
Because the effective Depth of Cut (Dcap), i.e. cutting diameter at cutting depth ap, is much narrower at the cutting point than the diameter of the tool which allows you to use large tools.

Engraving Case Study 1
Data Colibri G-JET Steel 250HB | |
---|---|
PRESSURE | 25 BAR |
FLOW RATE | 18 l/min |
RPM | 30.000 r/min |
Cutting Diameter | 2mm |
Cutting Tool | Spherical cutter with 2 cutting edges |
Data: | N= 30.000 RPM/min f= 0,03 mm/turn |
Vf= 1.000 mm/min ap= 0,3 mm ae= 0,5 mm |
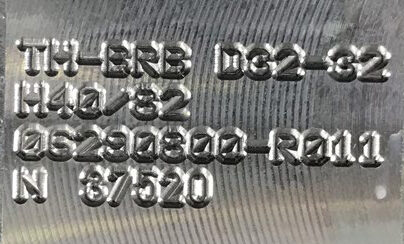
Engraving Case Study 2
Data Colibri HPC JET Brass | |
---|---|
PRESSURE | 70 BAR |
FLOW RATE | 24 l/min |
RPM | 45.000 r/min |
Cutting Diameter | 5mm |
Cutting Tool | Single Flute Solid Carbide 60° |
Data: | N= 37.000 RPM/min f= 0,015 mm/turn |
Vf= 700 mm/min ap= 0,4 mm ae= 0,4 mm |
ROI Analysis
Details | Machine Spindle | HPC Jet Spindle |
---|---|---|
Cutting Speed (m/min) | 113 | 700 |
Spindle Speed (min-1) | 5,995 | 37,136 |
Table Feed (mm/min) | 90 | 557 |
Metal Removal Rate (cm3/min) | 0.01 | 0.09 |
Cutting Time/Part (sec) | 234 | 38 |
Total machining cost per part(€) | 11.18 | 4.66 |
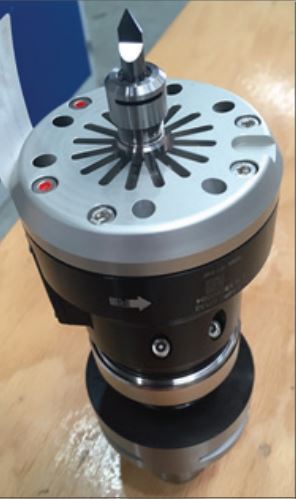